Коэффициент трения при прокатке реферат
Обновлено: 02.07.2024
С целью снижения сил трения, а следовательно, снижения интенсивности износа валков и энергосиловых параметров при горячей и холодной прокатке применяют различные технологические смазки (масла и эмульсии). Технологическая смазка захватывается валками и принудительно нагнетается в очаг деформации при вращении валков и движении полосы. В условиях прокатки со смазками в очаге деформации существует так называемое смешанное (полусухое или полужидкостное) трение, когда на контакте одновременно существуют участки сухого, граничного и жидкостного трения. Сухое трение в обычном процессе прокатки возникает в локальных точках взаимодействующих поверхностей и оно является основной причиной разрушения неровностей и износа поверхностей валков. На участках граничного трения поверхности разделены тонким и прочным слоем масляной пленки, имеющей в своем составе поверхностно активные вещества (ПАВ) в виде, например, жирных кислот. При граничном трении отсутствует непосредственный металлический контакт поверхностей валков и полосы. При жидкостном трении поверхности разделены относительно толстым слоем смазки, толщина которого превышает суммарную высоту неровностей поверхностей валка и полосы.
Таким образом, в общем случае среднее касательное напряжение трения на контакте может быть представлено следующим образом :
t = ac × tc + aг × tг + aж × tж ,
где tc, tг, tж – контактные касательные напряжения соответственно сухого, граничного и жидкостного трения; ac, aг, aж – относительные доли площади контакта с соответствующими напряжениями трения.
Известно, что между касательными напряжениями трения существует такое соотношение: tc > tг > tж. То есть изменение условий прокатки в сторону увеличения доли жидкостного трения (aж) приводит к общему снижению силы трения на контакте. Напряжение трения и ее составляющие определяются условиями прокатки: шероховатостью поверхностей валков и полосы, окружной скоростью валков, величиной обжатия, типом технологической смазки и некоторыми другими факторами.
Рис 4.16. Влияние скорости валков на коэффициент внешнего трения при холодной прокатке полос стали ст.08пс с размерами 0,83-1,57мм на реверсивных станах 1200 и 1680. Шероховатость валков R, мкм: 1-0,65; 2-1,8; 3-3,8.
Значение точности определения кинематических и энергосиловых параметров при горячей прокатке полос. Расчет базового коэффициента трения. Изменение коэффициента трения в зависимости от температуры. Расчет коэффициента трения при холодной прокатке полос.
Рубрика | Физика и энергетика |
Вид | реферат |
Язык | русский |
Дата добавления | 04.12.2015 |
Размер файла | 227,8 K |
Студенты, аспиранты, молодые ученые, использующие базу знаний в своей учебе и работе, будут вам очень благодарны.
Расчет коэффициента и показателя трения
Горячая прокатка полос. Коэффициент трения показывает интенсивность действия сил трения в очаге деформации, а его величина определяет значения опережения, энергосиловых параметров, износ валков, качество поверхности полосы. Точность определения кинематических и энергосиловых параметров во многом зависит от точности расчета коэффициента трения. Известны эмпирические формулы И.М. Павлова и H. H. Гета, М.А. Зайкова, А Динника, А.П. Грудева и др. для расчета коэффициента трения, полученные исследователями для конкретных условий прокатки на лабораторных станах. Это ограничивает или исключает их применение в промышленных условиях. А.П. Грудев предлагает использовать для расчета коэффициента трения зависимость, полученную на основании лабораторных исследований И.М. Павлова и H. H. Гета дополнительными поправочными коэффициентами [1,2]
- температура металла,°С; - поправочные коэффициенты, учитывающие соответственно влияние состояния и материала валков, окружную скорость валков, материал прокатываемой полосы (содержание углерода). Коэффициентравен: чугунные отбеленные валки - 0,9; чугунные мягкие - 1,0; стальные - 1,1 - 1,2; стальные с насечкой - 1,3-1,6. Коэффициент может быть определен по выражению
коэффициент трение прокатка полоса
где -окружная скорость валков. Влияние содержания углерода в стали описывает выражением
где - содержание углерода в стали,%.
В работе А.А. Динника [3] предложено следуют выражение для расчета коэффициента трения
где -базовый коэффициент трения, метод определения которого в работе не сообщается.
Базовый коэффициент трения на основании обработки данных [3] равен
где - скорость скольжения металла в очаге деформации,
где Д h и h-абсолютное обжатие и толщина полосы после прокатки
Коэффициент kм равен: для низкоуглеродистой стали - 1,0; для высокоуглеродистых сталей - 0,9-1,0; для нержавеющей стали - 1,1-1,2.
Наиболее достоверные значения коэффициента трения могут быть получены в том случае, если основные составляющие основного расчетного выражения получены в промышленных условиях наиболее теоретически обоснованными методами, т.е. методом опережения и методом крутящего момента с плавным торможением полосы в валках. Этому условию отвечают экспериментальные зависимости п.2.6, используя которые получена обобщающая формула (В.А. Николаев) расчета коэффициента трения в установившемся процессе [5,6,7]
(3)
где - базовый коэффициент трения, полученный на основании
промышленных исследований; -поправочные коэффициенты, учитывающие соответственно состояние поверхности валков, твердость валков, материал полосы, окружную скорость валков, тип технологической смазки, состояние окалины на
поверхности полосы, относительное обжатие.
Базовый коэффициент равен
где t - температура металла,°С.
Другие поправочные коэффициенты равны:
где HSD - твердость поверхности валков по Шору; - окружи скорость валков
Характеристика валков Коэффициент kB
Новые стальные и чугунные отбеленные 0,75
Чугунные и стальные валки после двух 1,0
Изношенные чугунные валки 1,15-1,2
Стальные валки с насечкой (накаткой) 1,2-1,4
Материал полосы Коэффициент kм
Ст.3, 08 кп (пс), ШХ-15-1,0
30ХГСА, А12 - 0,85
1Х18Н9Т,45Г17ЮЗ, ЭИ-654 1,08
1Х17Н2, Х17 - 1,15
Тип технологической смазки Коэффициент ксм
Эмульсия минерального масла 0,9
Эмульсия из ПХМ
(полимеризованное хлопковое масло) 0,8
Состояние окалины Коэффициент kок
C воздушной вторичной окалиной 1,0
С печной окалиной 0,6-0,7
Относительное обжатие Коэффициент kе
е> 30 - 1,1, е = 1,0. Формулы: 1- (1); 2- (2); 3- (3)
Как следует из данных рис.1, имеет место существенное различие между коэффициентами трения, определенными по формулам (1) - (3). Наименьшие значения коэффициента трения получены по формуле (1), а наибольшие по формуле (2). Между этими зависимостями существует почти двухкратное различие. Принимая во внимание хорошее совпадение с опытными промышлиными данными, зависимость (3) следует считать более достовернойи [8] и рекомендовать к практическому использованию.
При захвате переднего конца полосы валками условия трения отличны то таковых в установившемся процессе. Во-первых при соприкосновении полосы с валками образуется небольшая площадка контакта, во-вторых, скольжение происходит при отсутствии печной окалины, в-третьих, отсутствует пластическая деформация металла, в четвертых, как правило, задача полосы происходит с некоторой силой от рольганга или предыдущей клети, в-пятых, при скольжении по полосе в ряде случаев происходит удаление слоя окалины и появление чистого металла, в-шестых, поверхность трения площадки полосы охлаждается от валков и воды. Все это обусловливает повышен коэффициента трения fз при захвате по сравнению с коэффициеи трения fв установившемся процессе. Для расчета коэффициент трения при захвате можно использовать формулу
где f - коэффициент трения по формуле (3) при и kе =1,0
- коэффициент, учитывающий условия захвата и тип стана: Блюминг, слябинг, толстолистовой стан, черновые клети непрерывных широкополосных станов горячей прокатки (НШСГП) -
Непрерывные заготовочные станы, непрерывные группы НШПСГП
Холодная прокатка полос. В работе [1,9] приведены ряд формул для расчета коэффициента трения при холодной прокатке полос, о которых А.П. Грудев замечает, что они относятся к частным случаям экспериментов. На основании собственных исследований А П Грудев предлагает насколько формул для расчета коэффициента трения при прокатке соответственно в гладких (полированных шероховатых и грубошероховатых валках. Так, например, для прокатки в шероховатых валках Rz = 1,6-6,3 мкм (Rб, = 0,32-1,25 мкм предлагается следующая формула (холодная прокатка)
где _ коэффициент, учитывающий влияние типа технологической смазки; Rz - шероховатость поверхности валков; v - окружная скорость: валков; v50 - кинематическая вязкость смазки при 50°С с Ст (м 2 /с-10 -2 )
Указанная формула получена для расчета коэффициента трения при прокатке с чистыми маслами. Коэффициент для растительных масел равен для минеральных - , для эмульсий минерального масла можно принимать кинематическая вязкость v50 при 50?C для масел равна:
минеральная эмульсия - 20;
На основании лабораторных исследований Д.И. Старченко и др. предлагает следующую формулу для расчета коэффициента трения
где - коэффициент трения при ползучей скорости прокатки; - окружная скорость валка; -коэффициенты: ; .
В результате экспериментальных исследований влияния различных факторов на условия трения. При этом во всех экспериментах коэффициент трения определяется методом опережения с учетом упругих деформаций валков и полосы, а сами упругие деформации также определены экспериментально (и в лабораторных и в промышленных условиях) [10]. Расчетная формула коэффициента трения представлена следующим образом (В.А. Николаев):
где - базовый коэффициент трения, определенный в промышленных условиях; - поправочные коэффициенты, учитывающие соответственно величину относительного обжатия, шероховатость поверхности полосы и типа технологической смазки; - коэффициенты учитывающие влияние температуры полосы и различие в условиях деформации металла в промышленных и лабораторных исследованиях.
Коэффициент по данным [1, 11] равен
Тип смазки
Эмульсия минерального масла - 1,0
Хлопковое натуральное масло - 0,94
Подсолнечное гидрогенизированное масло (ПКС) 0,85
Пальмовое масло - 0,83
Хлопковое полимеризированное масло (ПХМ) - 0,56
Базовый коэффициент - определен в промышленных условиях учитывает влияние окружной скорости валков и шероховатости полосы:
Коэффициент влияния обжатия зависит от шероховатости валков. Поэтому:
где - относительное обжатие в долях; - шероховатости поверхности полосы; - коэффициент, учитывающий окружности скорость валков при .
В исследованиях [11,12,13,14] показано, что при прокатке с маловязкими смазками (индустриальное 12) характер зависимостей; коэффициента трения в области температур 20-250 С обусловлен величиной относительного обжатия. При прокатке с вязкими технологическими смазками (касторовое масло, масло вапор, ТЭМП-1) коэффициент трения существенно возрастает с увеличением температуры полосы. Аппроксимация опытных данных позвони получить уравнение вида (D=256мм, Н=1,08 и 2,5мм, сталь 08| Rа ? 0,8мкм):
где температура начала прокатки;
для эмульсий и маловязкого минерального масла (е ? 0.2):
дня высоковязкой смазки (е = 0,3): ; ; .
Расчет по приведенным выше формулам коэффициента трения для условий прокатки работы [9,15] (D = 256мм, v = 0,3м/с, Ra = 0,8 мкм tн= 25 С, смазка из минерального масла И-20А) дает следующие результаты:
Л.И. Грудева - 0,143
Д.И. Старченко - 0,098
Н.А. Николаева - 0,087
Опытные значения коэффициента трения при прокатке полос с обжатием е=0,3 равны [9,15]. Как следует из сопоставления меньшее отклонение от опытных данных получено при исследовании, формулы (4).
Отсутствие точного совпадения опытных и расчетных значений коэффициента трения, в частности по формуле (4), объясняется неадекватность условий деформации металла на лабораторных и промышленных станах при проведении исследований (различие диаметров валков, упрочнения полос, шероховатостью полос, чистоты смазки, температуры валков, отсутствием натяжения в лабораторных экспериментах) [9]. Влияние указанных различий при расчете коэффициента трения в лабораторных условиях предлагается учитывать поправочным коэффициентом kл, который равен [9]
В ряде случаев для расчета среднего нормального напряжения, вместо коэффициента трения, используют показатель трения. Ранее показано, что между показателем и коэффициентом трения существует тесная связь. Поскольку в обычных условиях прокатки то имеем. Отношение вида может быть лишь при прокатке - с высоковязкими технологическими смазками при рср/рф
Проблемы трения при прокатке металлических материалов.
Москва
2016 г.Содержание
1. Введение
2. Прокатка
3. Механизм сухого и жидкостного трения. Трение при различных видах ОМД
4. Силы трения при прокатке
5. Проблемы трения при прокатке
6. Литература
Производство металла имеет большое значение для развития народного хозяйства и роста благосостояния людей. От успешного развития металлургии в значительной мере зависит обеспечение металлом машиностроения,машиностроительства, транспорта, сельского хозяйства и других областей народного хозяйства. Технологический процесс получения готового проката является завершающей стадией металлургического производства. Через прокатные цеха проходит почти вся сталь, выплавляемая в сталеплавильных цехах, поэтому наряду с увеличением производства проката существует проблема повышения эффективности прокатного производства икачества готового продукта. Особенностью развития прокатного производства является переход к непрерывным процессам прокатки. Это позволяет существенно увеличить производительность прокатных станов и качество их продукции. Обеспечение непрерывной схемы прокатки требует существенного повышения уровня автоматизации технологических процессов и обеспечения оптимальности управления.
Управление технологическимпроцессом, проблема выбора оптимальной технологии связаны с выбором критерия оценки качества. Задачу выбора таких критериев можно определить как задачу определения качества технологическогопроцесса.
2.Прокатка
Прокатка - процесс ОМД, при котором заготовка под действием сил трения втягивается меду вращающимися валками прокатного стана и пластически деформируется ими с уменьшением сечения. Продольнойпрокаткой (рис. 1 ) прокатывается до 90% всей выплавляемой стали. Условие возникновения процесса прокатки определим из проекции действующих сил при прокатке, рис.1:
где m – коэффициент трения;
Для осуществления прокатки необходимо, чтобы коэффициент трения между валками и заготовкой был больше тангенса угла захвата: при горячей прокатке α = 15 – 24 0; при холодной прокатке α = 3– 8 0.
3.Механизм сухого и жидкостного трения. Трение при различных видах ОМД
Трение называют сухим, если поверхности обрабатываемого материала и инструмента находятся во взаимном контакте, свободны от третьих веществ и происходит относительное перемещение этих поверхностей в касательной к ним плоскости. В чистом виде такой вид трения при ОМД не встречается, поэтому на практике сухим трениемназывают трение несмазанных тел. Так, горячую прокатку проводят без смазки, поэтому трение при горячей прокатке условно называют сухим.Трение называют жидкостным, если между трущимися поверхностями имеется слой смазки, выводящий из механического зацепления шероховатости этих поверхностей Жидкостное трение - это внутреннее трение в объеме смазки. Оно нашло применение, например, при волочении проволоки. Ведутсяработы по реализации этого вида трения в других процессах ОМД. Термин “жидкостное” трение условен, так как смазка может быть консистентной и даже твердой, например парафин. Главное, чтобы не происходило соприкосновение трущихся поверхностей, а сопротивление деформации самой смазки было во много раз меньше сопротивления де-формации обрабатываемого металла. В практических условиях ОМД как сухое, таки жидкостное трение в чистом виде встречается редко. Это объясняется тем, что, с одной стороны, на металлическую поверхность всегда попадают вещества, препятствующие возникновению сухого трения. С другой стороны, при наличии даже обильной смазки в процессе деформирования металла происходит выдавливание смазывающей пленки, а также разрушение и потеря ее физических.
Контактное трение оказывает значительное влияние на процесс пластической деформации. Одновременно с полезным действием трение вызывает затруднение в технологии изготовления изделий.
Коэффициент трения зависит от ряда факторов – материала поверхности валков, температуры прокатываемого металла, скорости прокатки, химического состава прокатываемой полосы.
При определении коэффициента трения применяют следующие основные формулы:
где угол трения
Формула С. Экелунда:
где коэффициент, учитывающий влияние материала валков;
для стальных валков
для чугунных валков
t – температура металла,
Формула Б. П. Бахтинова и М. М. Штернова:
где коэффициент, учитывающий влияние окружной скорости валков (определяется по графику, приведённом на рисунке 3).
![]() |
Рисунок 3 – Значение ![]() для расчёта коэффициента трения |
44 |
Таблица 20 – Значение коэффициента ![]() при прокатке сталей различных марок |

– коэффициент, учитывающий влияние химического состава прокатываемой стали (определяется по табл. 20)
Группа стали | Марка стали | Коэффициент ![]() |
Низкоуглеродистая | Ст.1 | 1,0 |
Ледебуритная | Р18 | 1,10 |
Перлитно-мартенситная | ШХ15 | 1,24 - 1,30 |
Аустенитная | 4Х13 | 1,40 |
Аустенитная с избыточной фазой | Х13Н4Г9 | 1,45 |
Ферритная | Х18Н10Т | 1,55 |
Аустенитная с карбидами | 1Х17ЮА Х15Н60 | 1,60 |
Формула А. П. Грудева (при холодной прокатке):
где окружная скорость валков, ;
коэффициент, учитывающий влияние смазки (определяется по таб. 21)
45 |
Смазка | f | ![]() |
Сухие чистые валки | 0,086 | 1,55 |
Машинное масло | 0,075 | 1,35 |
Веретенное масло | 0,070 | 1,25 |
Вода | 0,058 | 1,0 |
Эмульсия (!0% масла) | 0,056 | 1,0 |
Керосин | 0,053 | 1,0 |
Хлопковое масло | 0,051 | 0,9 |
Касторовое масло | 0,050 | 0,9 |
Пальмовое масло | 0,048 | 0,9 |
46 |
Определите коэффициент трения по формуле Б. П. Бахтинова при различных температурах и постройте график зависимости коэффициента трения от температуры полосы.
Таблица 22 - Исходные данные
№ варианта | Материал валков | Скорость прокатки, ![]() | Материал полосы | Температура прокатки, t, ![]() |
1 | сталь | 3,0 | Сталь ст.3 | 1270; 1150; 1000; 900 |
2 | сталь | 3,4 | ШХ 15 | 1230; 1180; 980; 920 |
3 | сталь | 4,0 | Сталь ст.1 | 1280; 1220; 1050; 950 |
4 | сталь | 4,2 | 4Х13 | 1180; 1220; 1050; 950 |
5 | сталь | 3,5 | Сталь ст.3 | 1220; 1180; 1120; 1000 |
6 | чугун | 3,9 | Р18 | 1000; 980; 950; 920 |
7 | чугун | 4,2 | Х15Н60 | 1100; 1080; 1000; 950 |
8 | чугун | 4,6 | Х13Н4Г9 | 1060; 1020; 1000; 960 |
9 | чугун | 4,7 | 4Х13 | 1020; 980; 960; 900 |
10 | чугун | 5,2 | Сталь ст.1 | 1010; 990; 940; 910 |
47 |
![]() |
t, ![]() |
Рисунок 4 – График зависимости коэффициента трения от температуры |
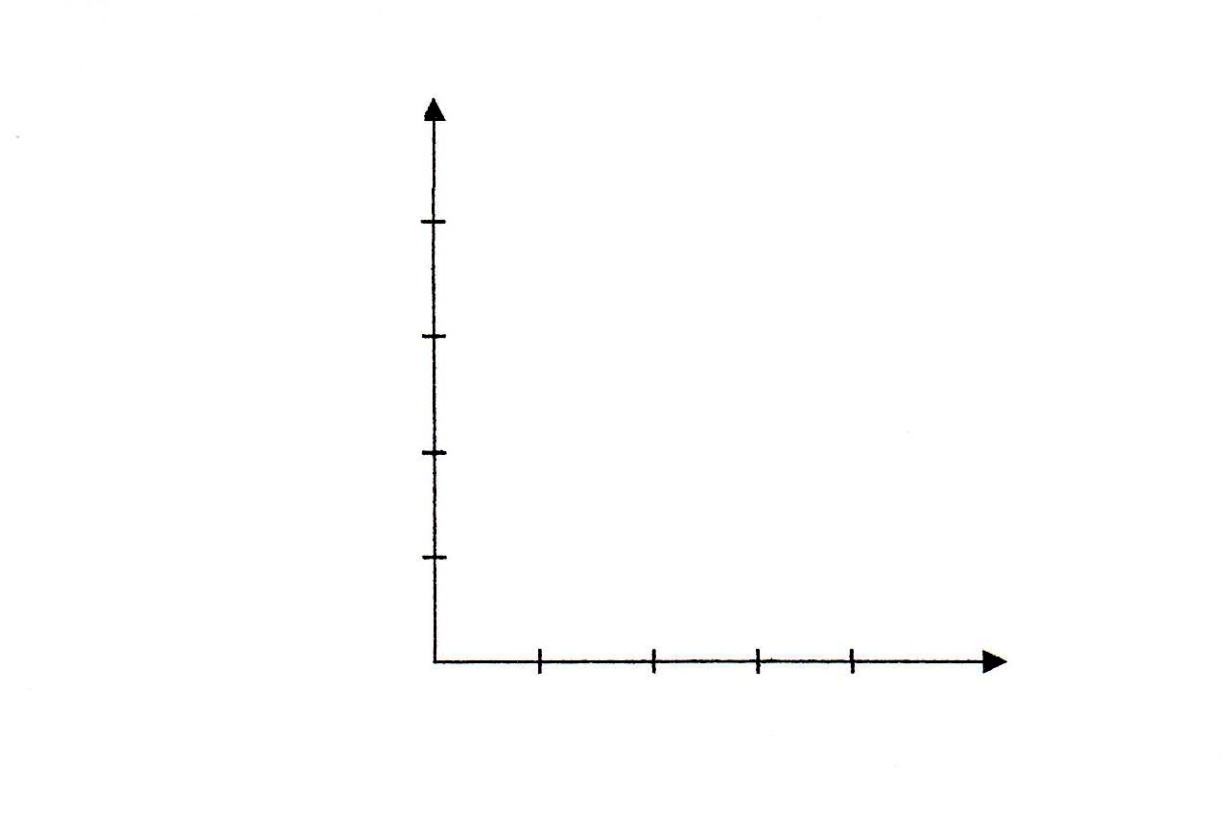
По результатам расчетов сделать вывод.
48 |
Определите коэффициент трения по формуле Б. П. Бахтинова при различных скоростях прокатки и постройте график зависимости коэффициента трения от скорости прокатки.
Таблица 23 - Исходные данные
№ варианта | Материал валков | Материал полосы | Температура прокатки, t, ![]() | Скорость прокатки, ![]() м/с |
1 | сталь | Сталь ст.3 | 1250 | 1,0; 2,0; 3,0; 4,0; 10,0 |
2 | сталь | ШХ 15 | 1230 | 1,2; 1,8; 3,2; 4,0; 8,0 |
3 | сталь | Сталь ст.1 | 1200 | 1,3; 2,0; 4,5; 6,0; 10,0 |
4 | сталь | 4Х13 | 1180 | 0,8; 1,2; 1,8; 3,0; 6,0 |
5 | сталь | Сталь ст.3 | 1160 | 1,5; 2,5; 4,0; 8,0; 10,0 |
6 | чугун | Р18 | 1040 | 1,1; 2,3; 4,0; 6,2; 8,0 |
7 | чугун | Х15Н60 | 1020 | 1,2; 3,0; 4,0; 4,5; 5,0 |
8 | чугун | Х13Н4Г9 | 1000 | 1,0; 2,2; 4,2; 5,5; 6,0 |
9 | чугун | 4Х13 | 980 | 1,3; 1,8; 2,6; 3,4; 5,2 |
10 | чугун | Сталь ст.1 | 920 | 1,0; 2,5; 3,5; 4,5; 10,0 |
![]() |
![]() , ![]() |
Рисунок 5 - График зависимости коэффициента трения от скорости прокатки |
49 |
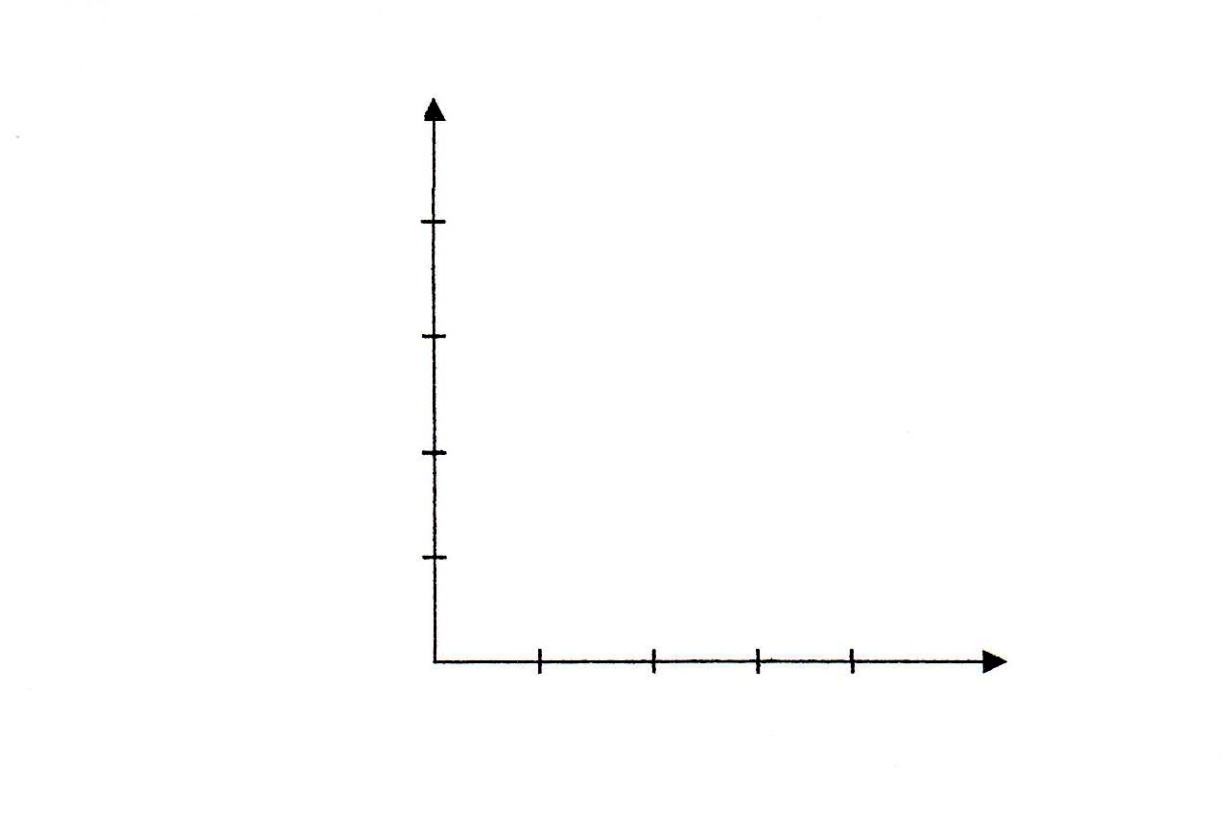
По результатам расчетов сделать вывод.
50 |
Определите коэффициент трения при холодной прокатке листов
Таблица 24 - Исходные данные
№ варианта | Скорость прокатки, ![]() | Смазка |
1 | 10 | Машинное масло |
2 | 12 | Веретенное масло |
3 | 15 | Вода |
4 | 18 | Эмульсия (10% масла) |
5 | 20 | Керосин |
6 | 22 | Хлопковое масло |
7 | 26 | Касторовое масло |
8 | 30 | Пальмовое масло |
9 | 35 | Эмульсия (10% масла) |
10 | 40 | Машинное масло |
51 |
Задача №1
Определите коэффициент трения в обжимной клети рельсобалочного стана. Условия прокатки следующие: стальные валки диаметром D = 950 мм, материал полосы сталь, Ст. 3, температура полосы t = 1200 ,
скорость валков 60 об/мин.
Задача №2
Определите коэффициент трения при холодной прокатке листов скорость прокатки 20 , смазка валков и листа производится хлопковым маслом.
Задача №3
Определите коэффициент трения при прокатке полосы (материал полосы – сталь Ст. 3) на стальных валках со скоростью 10 температура полосы
t = 900
Цель работы: ознакомиться с методикой определения коэффициента внешнего трения при захвате полосы валками и при установившемся процессе прокатки.
Лабораторное оборудование
Лабораторный стан (рис. 1) является одноклетьевым реверсивным станом для прокатки узких полос.
Рис. 1. Схема лабораторного прокатного стана:
1 – рабочая клеть; 2 – универсальные соединительные шпиндели;
3 – шестеренная клеть; 4 – коренная муфта; 5 – промежуточный вал;
6 – редуктор; 7 – двигательная муфта; 8 – главный электродвигатель
Рабочая клеть стана представляет собой клеть ДУО со станинами открытого типа. Прокатные валки стальные с диаметром и длиной бочки 120 и 150 мм соответственно.
Перемещение верхнего валка осуществляется с помощью нажимных винтов и электромеханического привода.
Привод вращения прокатных валков содержит главный электродвигатель постоянного тока, горизонтальный цилиндрический редуктор с передаточным числом 50, шестеренную клеть и универсальные шпиндели с шарнирами Гука.
Основные теоретические сведения
Внешнее трение играет важную роль в процессе прокатки, для осуществления которого должен произойти захват полосы вращающимися валками, возможный только при выполнении определенного условия (рис. 2).
Рис. 2. Схема силового взаимодействия
Полосы и валков при захвате
Из условия равновесия полосы под действием приложенных к ней сил следует, что сумма горизонтальных проекций сил должна равняться нулю:
где – сила трения; – сила нормального давления; –угол захвата.
Приведенное равенство можно представить в виде:
Сила трения является движущей силой при прокатке, поэтому захват произойдет только в том случае, если .
Известно, что сила трения и сила нормального давления связаны зависимостью
где – коэффициент внешнего трения при захвате.
Тогда условие захвата полосы валками можно представить в следующем виде:
При максимально возможном угле захвата имеет место следующее равенство:
Максимально возможный угол захвата можно определить по формуле:
где , – высота полосы до и после прокатки соответственно; – радиус прокатного валка.
При установившемся процессе прокатки (рис. 3) для определения условия равновесия полосы принимается допущение, что равнодействующая сил трения и нормального давления приложена посередине дуги контакта.
Рис. 3. Схема силового взаимодействия полосы и валков
Полоса будет находиться под действием приложенных к ней сил в равновесии при возникновении буксования валков, которое начинается после достижения максимально возможного абсолютного обжатия.
При этом имеет место следующее равенство:
где – коэффициент внешнего трения при установившемся процессе прокатки; – максимально возможный угол захвата при установившемся процессе прокатки. Для этого случая используются образцы клиновидной формы (рис. 4).
Рис. 4. Размеры клиновидного образца до прокатки
При прокатке тонких полос при отношении где – длина дуги контакта полосы с валком; – средняя толщина полосы в очаге деформации , коэффициент внешнего трения достаточно точно можно определить по опытным величинам опережения .
При прокатке скорость входа полосы в валки меньше горизонтальной проекции окружной скорости валков, а скорость выхода – больше. Это явление называется отставанием и опережением.
Отставание и опережение принято определять как относительную величину.
Опережение представляет большой практический интерес, т.к. позволяет рассчитать угловую скорость валков отдельных рабочих клетей непрерывных прокатных станов.
Опережение можно определить по формуле:
где – скорость полосы на выходе из валков; – окружная скорость валков.
Практически опережение определяют (рис. 4) после измерения расстояний между отпечатками кернов на полосе от кернов на поверхности валков по формуле:
Рис. 5. Схема прокатки образца
для определения опережения керновым методом
Теоретически для тонкой полосы опережение можно определить по формуле Дрездена:
где – толщина полосы после прокатки; – критический (нейтральный) угол.
По опытному опережению из формулы Дрездена определим нейтральный угол γ и коэффициент трения :
где – угол захвата; – толщина полосы после прокатки; – радиус прокатных валков.
Результаты экспериментального и расчетного определения величин заносятся в табл. 1.
Характер процесса прокатки | Измеряемые и расчетные величины | ||||||
h0,мм | h1, мм | , рад | S, % | , рад | |||
опыт | расчет по формуле А.П. Грудева | ||||||
Захват полосы | 19,8 | 15,2 | 0,27 | 14,8 | 1,93 | 0,85 | 0,087 |
Установившийся процесс | 23,8 | 0,27 | 14,8 | 1,57 | 0,85 | 0,087 |
Роль химии в жизни человека: Химия как компонент культуры наполняет содержанием ряд фундаментальных представлений о.
Примеры решений задач по астрономии: Фокусное расстояние объектива телескопа составляет 900 мм, а фокусное .
Как оформить тьютора для ребенка законодательно: Условием успешного процесса адаптации ребенка может стать.
Читайте также: