Колесная пара электровоза доклад
Обновлено: 18.05.2024
- превращают вращающий момент тяговых двигателей в поступательное движение электровоза.
Колесные пары воспринимают все удары от неровностей пути и сами жестко воздействуют на путь.
Основные элементы: ось 5, два колесных центра 1, два бандажа 2, два стопорных кольца 3 и два зубчатых колеса 4. (Рис.8).
Ось(рис.9). Изготавливается поковкой из осевой стали. Подвергается механической и термической обработке. Для упрочнения все ее части, кроме средней, накатываются роликами.
Ось имеет следующие части: 5-буксовые шейки, 4-предподступичные
Рис.8. Колесная пара электровоза ВЛ11.
части, 3 - подступичные части, 2 - шейки под моторно-осевые подшипники, 1 - средняя часть и галтели (плавные переходы от одного диаметра к другому)
- буксовые шейки служат для напрессовки внутренних колец двух буксовых подшипников.
Рис.9.Ось колесной пары.
1-средняя часть; 2-шейка под моторно-осевой подшипник; 3-подступичная часть; 4-предпдступичная часть; 5- буксовая шейка; 6-паз под стопорную пластину.
. На концах имеется резьба для корончатой гайки, а с торца - резьбовые отверстия для болтов стопорной планки;
- предподступичные части служат для напрессовки лабиринтного кольца задней буксовой крышки;
- подступичные части служат для напрессовки колесных центров;
-шейки под моторно-осевые подшипники для размещения вкладышей ;
-средняя часть соединяет все части оси.
После изготовления все части оси подвергаются магнитной дефектоскопии.
Колесный центр. Изготавливается отливкой из углеродистой стали. Имеет удлиненную ступицу 5, 12 спиц 6 и обод 7 (Рис. 10,а). Механической обработке подвергаются обод и ступица со всех сторон.
Рис.10. Колесный центр и бандаж.
1 -обод колесного центра, 2 - бандаж, 3 - стопорное кольцо, 4 - упорный бурт,
5 - ступица, 6 - спица,
Бандаж. (рис. 10,б) Изготавливается ковкой с последующей
прессовкой, механической и термической обработкой. Имеет уклоны:
1:20 - Исключает виляние колеса при движении его по прямому участку пути.
1:7 - Обеспечивает безопасный проход стрелочных переводов при наличии максимального проката (как часть бандажа, наименее изнашиваемая) , а также для частичного поглощения наката металла с поверхности катания.
Оба уклона совместно обеспечивают прохождение колесами в кривых различных отрезков пути за одинаковое время. Бандаж имеет фаску размером 6 мм х 45 0 для поглощения наката металла с поверхности катания.
Размеры нового бандажа: толщина 90+3 мм, ширина 140+2/1 мм, диаметр 1250 мм (измеренный по кругу катания), толщина гребня 3З мм (измеренная на расстоянии 20 мм от его вершины), высота гребня 30 мм, измеренная между вершиной и кругом катания.
Круг катания расположен на расстоянии 70 мм от грани бандажа. По нему производят основные измерения: диаметр бандажа, его толщину, прокат, ползун и толщину гребня.
После напрессовки бандажа на колесный центр, ставятся контрольные риски против одной из спиц на бандаже на расстоянии 24 мм 5-6 углублений керном и по ним полоса красной краской, и на колесном центре углубление зубилом и по нему полоса белой краской.
НЕИСПРАВНОСТИ КОЛЕСНЫХ ПАР.
Запрещается выпускать из ТО-2, ТО-3, ТР и допускать к следованию в поездах электровозы со следующими неисправностями колесных пар:
- трещинав любой части оси, ободе, спице или бандаже;
- прокатпо кругу катания у локомотивов более 7 мм при скорости до 120 км/час и более 5 мм при скорости 120-140 км/час;
- толщина гребня более 33 мм и менее 25 мм, при скорости до 120 км/час и более 33 мм и менее 28 мм при скорости 120-140 км/час, измеренная на расстоянии 20 мм от вершины гребня, при его высоте 30 мм. У колесных пар с высотой гребня 28 мм - 18 мм от вершины гребня. У 2 и 5 колесных пар электровозов ЧС2 более 23 мм и менее 21 мм, измеренная на расстоянии 16,25 мм от вершины гребня;
- толщина гребня у бандажей с новыми профилями до скорости 120 км/час для профиля ГОСТ 11018 более 32 мм и менее 23 мм Для профиля ДМеТИ более 31 мм и мене 2З мм. При скорости 120-140 км/час для профиля ГОСТ 11013 более 32 мм и менее 26 мм.
Для профиля ДМеТИ более 31 мм и менее 26 мм. Толщина гребни измеряется на расстоянии 13 мм от круга катания;
- разница в толщине гребней у одной колесной пары, если толщина одного из них 27 мм и менее, более 4 мм;
- расстояние между внутренними гранями бандажей у ненагруженной колесной пары 1440 +3/3 мм при скорости 120 км/час и +3/-1 мм при скорости 120-140 км/час;
- вертикальный подрез гребня более 18 мм, измеренный специальным шаблоном.
- опасная форма гребня (при значении параметра крутизны гребня 6,5 и менее), измеренная на ТР шаблоном УТ-1 и шаблоном ДО-1 на ТО-2.
- ползун (выбоина) на поверхности катания бандажа более 1 мм.
Скорость следования при ползуне более 1 мм см. в ПТЭ;
- выщербина, раковина или вмятина на поверхности катания бандажа глубиной более 3 мм и длиной более 10 мм, а выщербина на вершине гребня длиной более 4,0 мм;
- разница диаметров бандажей колесных пар в комплекте для электровозов в грузовом движении более 16 мм, у ЧС2 - более 12 мм;
- разница в прокатах у колес одной колесной пары более 2 мм;
- ослабление бандажа на колесном центре, оси в ступице, зубчатого колеса на оси или на ступице колесного центра;
- остроконечный накат гребня в зоне поверхности на расстоянии 2 мм от вершины гребня и 13 мм от круга катания;
- острые поперечные риски и задиры на шейках и предподступичных частях оси;
- протертое место на средней части оси более 4 мм;
- местное или общее уширение ширины бандажа более 6 мм;
- ослабление бандажного кольца в сумме на длине более 30%,более чем в трех местах, а также ближе 100 мм от замка кольца;
- толщина бандажей колесных пар электровозов ВЛ11, ВЛ11 м и ЧС менее 45 мм. В бесснежный период, с разрешения начальника дороги, 40 мм (кроме электровозов ЧС2);
- кольцевые выработки на поверхности катания у основания гребня глубиной более 1 мм на конусности 1:3,5 глубиной более 2 мм и шириной более 15 мм. При наличии кольцевых выработок на других участках поверхности катания бандажа нормы браковки как для кольцевых выработок расположенных у гребня.
Дефекты, обнаруженные при осмотре колесных пар, записать в журнал формы "ТУ-152 и в журнал ремонта электровоза формы ТУ-23. Не реже одного раза в месяц производить замеры проката, толщины бандажей, их гребней и опасной формы гребня. Результаты замеров за-
носить в журнал ТУ-28 и в карманную книжку обмера бандажей ТУ-13.
Примечание:
- под раковиной понимается дефект металлургического происхождения в виде неметаллических включений (песка, шлака) закатанных внутрь металла и пустот от усадки металла при неравномерном остывании бандажа выходящих на поверхность катания бандажа по мере износа;
- под выщербиной понимается выкращивание кусочков металла на поверхности катания бандажа;
Папиллярные узоры пальцев рук - маркер спортивных способностей: дерматоглифические признаки формируются на 3-5 месяце беременности, не изменяются в течение жизни.
Поперечные профили набережных и береговой полосы: На городских территориях берегоукрепление проектируют с учетом технических и экономических требований, но особое значение придают эстетическим.
Организация стока поверхностных вод: Наибольшее количество влаги на земном шаре испаряется с поверхности морей и океанов (88‰).
Вы можете изучить и скачать доклад-презентацию на тему Колесные пары. Презентация на заданную тему содержит 17 слайдов. Для просмотра воспользуйтесь проигрывателем, если материал оказался полезным для Вас - поделитесь им с друзьями с помощью социальных кнопок и добавьте наш сайт презентаций в закладки!
Ось имеет две буксовые шейки 1 (они служат для монтажа роликовых подшипников буксы), предподступичные части 2 (на них насаживают лабиринтные кольца осевой буксы), подступичные части (на них напрессовывают колесные центры), шейки моторно-осевых подшипников 4 и среднюю часть. Ось имеет две буксовые шейки 1 (они служат для монтажа роликовых подшипников буксы), предподступичные части 2 (на них насаживают лабиринтные кольца осевой буксы), подступичные части (на них напрессовывают колесные центры), шейки моторно-осевых подшипников 4 и среднюю часть. В конструкциях с приводом класса 2 у осей нет шеек для моторно-осевых подшипников. Оси испытывают напряжения, изменяющиеся по знакопеременному симметричному циклу. Особенно опасна концентрация напряжений, которая зависит от качества обработки поверхности, плавности переходов (галтель) между частями разных диаметров, условий запрессовки на ось сопрягаемых с нею деталей.
Ось унифицированной колесной пары электровозов ВЛ60, ВЛ80 и ВЛ10к : 1 — буксовая шейка; 2 — предподступичная часть; 3 — подступичная часть; 4 — шейка моторно-осевых подшипников.
Оси изготовляют из стали Ос. Л с последующим отпуском и должны соответствовать требованиям ГОСТ3281-81. Галтели выполняют с возможно большими радиусами и с повышенной чистотой обработки ее поверхности. Оси изготовляют из стали Ос. Л с последующим отпуском и должны соответствовать требованиям ГОСТ3281-81. Галтели выполняют с возможно большими радиусами и с повышенной чистотой обработки ее поверхности. Для повышения сопротивления усталости цилиндрические поверхности оси и их галтели (кроме средней части оси) упрочняют накаткой роликами с усилием 30-40 кН. При этом предел выносливости стали повышается примерно в 2 раза. После накатки шейки шлифуют. После обработки ось колесной пары подвергают контролю ультразвуковым и магнитным дефектоскопами, затем на торце оси ставят клейма.
Колесный центр действуют силы от посадки бандажа и запрессовки оси колесной пары; вертикальные и горизонтальные продольные и поперечные силы, действующие между бандажом и осью колесной пары. Применяют спицевые и дисковые (преимущественно литые) колесные центры. Спицевой колесный центр состоит из обода, спиц и ступицы (электровозы ВЛ19, ВЛ22м центр имеет 11 спиц ЧС2 и ЧС4 – 12 спиц). Колесный центр действуют силы от посадки бандажа и запрессовки оси колесной пары; вертикальные и горизонтальные продольные и поперечные силы, действующие между бандажом и осью колесной пары. Применяют спицевые и дисковые (преимущественно литые) колесные центры. Спицевой колесный центр состоит из обода, спиц и ступицы (электровозы ВЛ19, ВЛ22м центр имеет 11 спиц ЧС2 и ЧС4 – 12 спиц). Унифицированные колесные пары электровозов ВЛ10, ВЛ60, ВЛ80 имеют литые двухдисковые центры из углеродистой стали (в соответствии с ГОСТ 4491-86 из стали 20Л или 25Л) и имеют коробчатую конструкцию. Они состоят из удлиненной ступицы, обода и соединяющей их средней двустенной части. На обод колесного центра насаживают бандажи (диаметр посадочной поверхности 1070мм, при диаметре круга катания нового бандажа 1250 мм).
Диаметр посадочной поверхности колесного центра на ось 235 мм. Для уменьшения внутренних напряжений в оси при запрессовке колеса на ось посадочная поверхность расточена на конус со стороны зубчатого колеса 1. Центр колеса имеет канал с пробкой 4 для подачи масла под давлением для уменьшения усилия распрессовки. Для снятия внутренних напряжений и получения однородной и мелкозернистой структуры колесные центры подвергают отжигу. Диаметр посадочной поверхности колесного центра на ось 235 мм. Для уменьшения внутренних напряжений в оси при запрессовке колеса на ось посадочная поверхность расточена на конус со стороны зубчатого колеса 1. Центр колеса имеет канал с пробкой 4 для подачи масла под давлением для уменьшения усилия распрессовки. Для снятия внутренних напряжений и получения однородной и мелкозернистой структуры колесные центры подвергают отжигу. Механические характеристики должны быть: Предел текучести, мПа ……………………………245 Временное сопротивление разрыву, мПа……. 440. Для бандажных колес клейма ставят на наружном торце ступицы колесного центра (рис.) и на наружной грани бандажа (рис.), а у прицепных вагонов на наружной боковой поверхности обода цельнокатаного колеса (рис.)
Назначение. Колесные пары направляют электровоз или электропоезд по рельсовому пути, передают на автосцепку силу тяги, развиваемую локомотивом, и тормозную силу при торможении, воспринимают статические и динамические нагрузки, возникающие между рельсами и колесами, и преобразуют вращающий момент тягового двигателя в поступательное движение. Колесные пары жестко воспринимают все удары от неровностей пути в вертикальном и горизонтальном направлениях и сами жестко воздействуют на путь, поэтому в эксплуатации необходим тщательный уход за ними.
Колесную пару формируют из отдельных элементов: оси 1 (рис. 14 и 15), двух колесных центров 6 с бандажами или двух безбандажных колес, одного или двух (на электровозах и моторных вагонах) зубчатых колес. Условия работы существенно отличаются для различных элементов колесной пары, вследствие чего для каждого элемента выбирают такой материал, который более всего удовлетворяет этим условиям.
Классификация колесных пар. На электровозах с индивидуальным приводом оси имеют внешние шейки. Шейки осей колесных пар электровозов (с 1958 г.) и электропоездов выполняют под буксы с роликовыми подшипниками
По принципу насадки зубчатого колеса различают колесные пары типа I (рис.
14,6), у которых зубчатое колесо непосредственно насажено на ось, и типа II (рис. 14,а, и в, рис. 15,а), у которых зубчатое колесо закреплено на удлиненной ступице. В зависимости от конструкции колесного центра колесные пары делят на спицевые, дисковые и коробчатые. На электровозах и моторных вагонах электропоездов применяют колесные пары с литыми спицевыми (см. рис. 14), коробчатыми и дисковыми центрами, имеющими съемные бандажи. На прицепных вагонах электропоездов и электровозах ЧС200 используют колесные пары со стальными цельнокатаными колесами (рис. 15,6).
В соответствии с Правилами технической эксплуатации железных дорог Союза ССР (ПТЭ) каждая колесная пара электровоза и электропоезда должна иметь четко проставленные знаки о времени и месте ее формирования и полного освидетельствования, а также клейма о приемке ее при формировании. Порядок и расположение знаков и клейма установлены Инструкцией по освидетельствованию и формированию колесных пар локомотивов и электросекций (ЦТ 2306).
Колесные пары за время эксплуатации подвергают осмотру под электровозами или вагонами электропоезда, обыкновенному и полному освидетельствованию, а также освидетельствованию с выпрес-совкой оси. Машинист проверяет состояние колесных пар при каждом осмотре, а также после аварии, столкновения поезда или схода с рельсов. Обыкновенное освидетельствование колесных пар производят во всех случаях подкатки их под электровоз или вагон электропоезда, при обнаружении дефектов оси ультразвуком в процессе полного их освидетельствования, необходимости снятия колесных центров, а также в случае отсутствия или неясности клейма и знаков формирования согласно Инструкции по освидетельствованию и формированию колесных пар локомотивов и электросекций (ЦТ 2306).
Оси колесных пар. На оси колесных пар воздействуют большие знакопеременные нагрузки; изготовляют оси ковкой из специальной осевой локомотивной стали ОсЛ, временное сопротивление растяжению которой не ниже 590 МПа.
Рис 14. Колесные пары электровозов ВЛ10, ВЛЮ*, ВЛП ВЛ80\ ВЛ80% ВЛ80\ ВЛ80 Р (а), ЧС4 и ЧС4 т (б), ЧС2 и ЧС2 Т (в):
1 - ось, 2 и 5 - бандажи; 3 и 4 - зубчатые колеса, 6 - колесный центр коробчатого сечения; 7 - фасонное установочное кольцо, 8 - отверстие для подачи масла на посадочную поверхность ступнцы и оси перед распрессовкой колесного центра, 9 - втулка зубчатого колеса; 10-венец зубчатого колеса; П - лабиринтное кольцо редуктора
Ось имеет шейки под буксовые и моторно-осевые подшипники (при моторноосевой подвеске тяговых двигателей), предподступичные и подступичные части, среднюю часть. Всю поверхность оси колесной пары электровоза, за исключением торцов, а на электропоезде - за исключением шеек и подступичных час тей, шлифуют. Оси обрабатывают, доводя до соответствующих размеров, под запрессовку колесных центров (или колес) и посадку буксовых подшипников Переходы между частями различных диаметров выполняют плавно, чтобы не допустить концентрации напряжений. С целью повышения усталостной прочности упрочняют накаткой роликами (на специальных токарно-накатных станках) поверхности под буксовые, подступичные части и моторно-осевые подшипники При этом повышается микротвердость поверхностных слоев и меньше вероятность возникновения усталостных трещин на поверхностях, подвергающихся действию высоких динамических напряжений. Чтобы обнаружить скрытые трещины, оси после механической обработки проверяют магнитным дефектоскопом. Оси колесных пар прицепных вагонов изготовляют из осевой вагонной стали ОсВ (см. рис. 15,6).
Рис. 15. Колесные пары моторного (а) и прицепного (б) вагонов электропоездов ЭР2 и ЭР9М I - ось, 2 - бандаж, 3 - венец зубчатого колеса; 4 - колесо с центром, 5 - фасонное установочное (заводное) кольцо; 6 - колесный центр спнцевой конструкции с удлиненной ступицей, 7 - упорная крышка стакана, 8 - стакан длц установки редуктора; 9 - упорное кольцо, 10 - подшипник стакаиа передний; 11 - лабиринтная крышка стакана; 12 - дистанционное кольцо; 13 - подшипник стакана задний, 14 - цельнокатаное колесо
Колесные центры. Они отлиты из углеродистой стали 25 лШ, имеют либо коробчатую (электровозные, см. рис. 14), либо спицевую (моторные вагоны электропоездов, см. рис. 15,а) конструкцию.
Бандажи. При движении по рельсам на поверхности колес в точке контакта с рельсом возникают большие контактные напряжения под действием веса локомотива и передаваемых тяговых усилий; это приводит к большому износу поверхности катания. Из-за этого изнашиваемую часть колеса на электровозах и моторных вагонах выполняют в виде сменного бандажа. Диаметр бандажа для каждого подвижного состава определяют расчетом. При этом учитывают, что увеличение диаметра бандажа улучшает плавность и стабильность хода тележки, условия работы буксовых подшипников. Бандажи изготовляют из специальной бандажной стали с содержанием углерода 0,57-0,65%, временным сопротивлением не менее 850 МПа и твердостью не менее 243 НВ. Для предотвращения проворачивания на ободе колесного центра применяют горячую посадку бандажа (температура его нагрева 250- 320 °С) с натягом 1,1 -1,45 (для моторных вагонов) и 1,3-1,7 мм (для электровозов). Затем в канавку бандажа заводят выполненное из специального стального профиля кольцо 7 (см. рис. 14, а), препятствующее его поперечному сдвигу. Буртик канавки обжимают с помощью роликов на специальном прессе.
Профиль поверхности катания колес определен условиями прохождения колесных пар по закруглениям рельсового пути. При движении колесной пары по кривому участку пути одно из колес катится по внутреннему рельсу, второе - по наружному. Радиусы закругления наружного и внутреннего рельсов различаются на ширину колеи пути, наружный рельс длиннее внутреннего. Если бы колеса имели цилиндрические поверхности катания, то наружное колесо неизбежно отставало бы от внутреннего, которое катится по более короткому пути. Это привело бы к проскальзыванию колес по рельсам и, следовательно, к повышенному износу бандажей и рельсов, а также к ухудшению сцепления колес с рельсами.
Конический профиль поверхности катания уменьшает проскальзывание колес, так как под действием центробежной силы колесная пара перемещается в поперечном направлении и наружное колесо контактирует с рельсом по большему диаметру конической поверхности, а внутреннее - по меньшему Уклон профиля катания переменный: в основной части рабочей поверхности бандажа 1:20, в конце этой поверхности 1:7 (см. рис. 14,а и 15).
Бандажи с таким профилем при прижатии гребня к наружному рельсу взаимодействуют с ним в двух точках, где в основном возникает трение скольжения. Оно приводит к интенсивному износу гребня, особенно в начальный период эксплуатации бандажа, до образования проката 2-3 мм. Это вызывает необходимость преждевременной обточки бандажей и увеличение расхода металла. Поэтому ВНИИЖТом был предложен новый профиль бандажа (см. рис. 14,в), который введен с 1 января 1988 г. на сети дорог для тягового подвижного состава. Отличиями этого профиля являются: уменьшение до 28 мм высоты гребня против 30 мм по старому профилю, изменение угла наклона гребня с 70 до 65 °, увеличение с 13,5 до 15 мм радиуса перехода от гребня к кругу катания. Введена поверхность радиуса 70 мм, дополнительно включена в средней части круга катания конусность 1:50. При таком профиле бандаж контактирует с рельсом в одной точке, в которой между гребнем и рельсом возникает в основном трение качения. Износ гребня становится менее интенсивным, периоды между обточками увеличиваются, потери металла сокращаются.
Конический профиль бандажей облегчает проход стрелочных переводов колесами, имеющими значительный прокат. Фаска у наружного торца бандажа, выполненная под углом 45 °, служит для смещения на нее наплывов металла, образовавшихся при прокате поверхности катания.
Для контроля за положением бандажа относительно центра на наружную поверхность бандажа и обод центра наносят контрольные метки, расположенные по радиусу против одной из спиц. Контрольную метку на бандаже выполняют в виде четырех-пяти насечек глубиной 1,5 мм на длине 25 мм, а на ободе центра - зубилом в виде риски глубиной до 1 мм.
Формирование колесной пары. Собранное колесо запрессовывают на ось в холодном состоянии на горизонтальном гидравлическом прессе, оборудованном манометром и специальным прибором для снятия индикаторной диаграммы запрессовки. Давление запрессовки зависит от диаметра и длины сопрягаемых поверхностей, а также от выбранного натяга. По диаграмме, форму которой строго регламентируют, судят о правильности формирования колесной пары, осуществляемого в соответствии с инструкцией ЦТ 2306. Перед запрессовкой ось смазывают растительным маслом или его заменителем.
Заключение о прочности запрессовки колес делают по индикаторным диаграммам. При нормальной запрессовке индикаторная диаграмма представляет собой плавно нарастающую несколько выпуклую вверх кривую Р (/) по всей длине I участка запрессовки (здесь Р - давление). Колесную пару, для которой при запрессовке получена диаграмма, неудовлетворительная как по очертанию, так и по величине усилий запрессовки колес на ось, бракуют и распрессовы-вают
Колесная пара — основной элемент ходовых частей подвижного состава. Колесная пара вагонной тележки воспринимает нагрузку от вагона и служит для направления движения его по рельсовому пути (см. рис.). Состоит из двух цельнокатаных колёс, напрессованных в холодном состоянии на ось. На наружные концы оси через рессоры и буксы опирается рама тележки. Вагонное колесо состоит из ступицы, диска и обода.
У одного края обода, обращённого внутрь колесной пары, имеется гребень, предохраняющий её от схода с рельсов. Поверхности катания колеса придаётся коничность для устранения неравномерного проката по ширине поверхности катания и для облегчения движения по рельсам.
Вагонная ось состоит из шеек с подшипниками качения или скольжения, а также подступичных частей, на которые напрессовываются колёса. Для смягчения перехода от подступичных частей к шейкам служат предподступичные части. Переходы между частями выполняются в виде галтелей.
Колесные пары локомотивов входят в колёсно-моторный блок.
Рис. 2. Колесная пара с роликовыми буксовыми узлами
Видно, что на цилиндрический стержень (ось) неподвижно установлены (напрессованы) на определенном расстоянии два колеса, а на концевых частях оси (шейках) смонтированы буксовые узлы.
Масса колесной пары составляет 1250 кг.
Колесная пара является наиболее ответственной частью вагона, так как передает все нагрузки от кузова на железнодорожный путь и обеспечивает безопасное движение по нему с заданной скоростью.
1 — расстояние между внутренними гранями колес; 2 — диаметр колеса по кругу катания;
3 — диаметр шейки оси; 4— диаметр предподступичной части оси; 5 — диаметр средней части оси;
6 — размеры элементов
Конструктивно элементы колесной пары выполняются следующим образом (рис. 3).
Рис. 4. Элементы колесной пары
Ось колесной пары представляет собой цилиндрический стержень, имеющий разные диаметры частей по длине в зависимости от их назначения и воспринимаемых нагрузок (рис. 4).
На оси выделяются следующие части: шейки, предподступичные части, подступичные части и средняя часть оси.
Шейки служат для размещения и закрепления на них буксовых узлов. Для этого на торцах шеек предусматривается резьба или отверстия для болтов.
На подступичные части оси под большим давлением напрессовываются колеса. Эти части являются наиболее утолщенными по всей оси.
Для смягчения перехода от подступичных частей к шейкам служат предподступичные части. Кроме того, на предподступичной части размещается задний затвор буксы. Переходы от одной части оси к другой выполняются в виде галтелей (плавных переходов) соответствующего радиуса, за исключением перехода к средней части оси. Галтели резко снижают концентрацию напряжений при переходе от одного диаметра оси к другому и тем самым повышают надежность работы оси.
Колесо (рис. 5) имеет обод, диск и ступицу. Ширина обода — 130 мм. Переход от ступицы к ободу выполнен в форме диска, расположенного под некоторым углом к этим частям, что придает колесу упругость и снижает воздействия динамических сил. Диск слегка конусный: у ступицы его толщина больше, чем у обода. Такая форма распределения металла наиболее рациональна, так как обеспечивает равнопрочность колеса относительно поперечных толчков.
Рис. 6. Профиль поверхности катания колеса
У одного края обода колеса, обращенного внутрь колесной пары, имеется гребень, предохраняющий колесную пару от схода с рельсов. Гребень у вагонных колес имеет высоту 28 мм, толщина же его, измеренная на расстоянии 18 мм от вершины равна 33 мм.
Поверхности катания колеса придается коничность для выравнивания неравномерного проката по ширине поверхности катания, а также для облегчения прохождения кривых участков пути (рис. 6).
Профиль поверхности катания колес выбирается в соответствии с профилем головок рельсов и с учетом подуклонки рельсов, которая обеспечивается конусными подкладками под основание рельсов (рис. 7, 8).
Рис. 7. Схема взаимодействия колеса и рельса
Рис. 8. Схема укрепления рельса на шпале
У современных конструкций пути головке рельсов придается выпуклая форма, чтобы колесо катилось по ее середине. Рельсы устанавливаются с уклоном внутрь колеи, равным коничности поверхности катания колеса 1/20, благодаря чему давление от колеса на подошву рельса передается по вертикальной оси рельса, проходящей через его центр тяжести.
Начиная от гребня (рис. 6) после небольшой площадки, поверхность катания обода колеса имеет уклон 1/20, а затем 1/7, который оканчивается фаской 6x6 мм. Двойная коничность делается потому, что в обычных условиях колесо работает на коничности 1/20, а при проходе кривых участков включается конусность 1/7 и обеспечивается движение колесной пары с меньшим проскальзыванием колес. Кроме того, наличие конусности 1/7 и фаски 6x6 мм поднимает наружную грань колеса над головкой рельса, что обеспечивает беспрепятственный проход стрелочных переводов, даже при наличии нормированного проката поверхности катания колес.
Так как при конической форме поверхности катания колесо в разных местах имеет различные диаметры, то под диаметром колеса принято понимать диаметр круга, расположенного от внутренней (гребневой) грани колеса на расстоянии 70 мм. Этот круг называют кругом катания колеса. В его плоскости измеряется толщина обода колеса.
Для обеспечения безопасного движения колесной пары в рельсовой колее строго регламентируется расстояние между внутренними гранями колес. Для современных колес это расстояние установлено равным 1440 мм с допуском ±3,0 мм, причем оба колеса должны находиться на одинаковом расстоянии от середины оси.
При изготовлении всех элементов колесных пар предусмотрено их клеймение, указывающее место и время изготовления, номера элементов, плавки и т. д.
В вагонах устанавливаются только такие колесные пары, которые удовлетворяют требованиям специальной инструкции по освидетельствованию, формированию и ремонту вагонных колесных пар.
Обратите внимание
Колесо при качении по рельсу взаимодействует с ним на достаточно небольшой площадке (пятне), где реализуются чрезвычайно большие давления и напряжения. Это приводит к износам и даже отколам поверхности катания колес и рельсов.
Износы (прокат) и другие неисправности колесных пар вызывают увеличенные динамические силы, воздействующие как на вагон, так и на железнодорожный путь, угрожая безопасности движения поездов.
Основные возможные неисправности колесных пар приведены на рис. 9-12.
Рекомендуется подробно проанализировать и запомнить эти неисправности колесных пар, так как наличие таких неисправностей угрожает безопасности движения поездов.
Рис. 9. Основные неисправности колесных пар
Ползун (плоское место) глубиной более допускаемой
Выщербины (выкрошившиеся участки поверхности качания более допускаемых размеров или с наличием в них трещин или расслоений, идущих вглубь металла):
Колесная пара направляет электровоз по рельсам, передает силу тяги, развиваемую электровозом, и тормозную силу при торможениях, воспринимает статические и динамические нагрузки, возникающие между рельсом и колесом, и преобразовывает вращающий момент тягового электродвигателя в поступательное движение электровоза.
Технические характеристики колесной пары: Номинальный диаметр по кругу катания, мм 1250 Расстояние между внутренними гранями бандажей, мм 1440 Ширина бандажа, мм 140 Толщина нового бандажа по кругу катания, мм 90 Толщина изношенного бандажа по кругу катания, мм 45 |
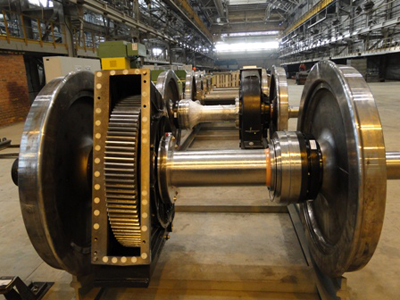
Рисунок 25. Колесная пара.
Ось колесной пары кованая из специальной осевой стали. Для монтажа буксовых подшипников, колесных центров, ступицы зубчатого венца, моторно-осевого подшипника со стороны противоположной редуктору на оси имеются специально обработанные участки. Все поверхности, заисключением торцов, подвергнуты шлифовке и упрочнению. После окончательной механической обработки ось колесной пары подвергается неразрушающему магнитному и ультразвуковому контролю.
1 – ось колесной пары; 2 – колесный центр; 3 – моторно-осевой подшипник стороны редуктора; 4 – бандаж; 5 – венец зубчатого колеса;
6 – ступица зубчатого колеса;7 – моторно-осевой подшипник.
Рисунок 26. Колесная пара.
На электровозе 2ЭС10 применена колесная пара с дисковым цельнокатанным колесным центром. Центра колесных пар изготовлены из стали химический состав которой соответствует техническим условиям по заготовке катанных колесных центров. Колесные центра перед насадкой на ось проверяются на отсутствие трещин.
Бандаж изготовлен из специальной стали, на обод колесного центра посажен в горячем состоянии, для предупреждения сползания застопорен бандажным кольцом. Профиль бандажа соответствует профилю, принятому для локомотивов. Перед насадкой бандаж проверяется на отсутствие трещин.
Читайте также: